La identificación rápida de fallas potencialmente dañinas (y la identificación de las causas raíz) dieron como resultado ganancias significativas en la productividad y el control de calidad para esta hilatura.
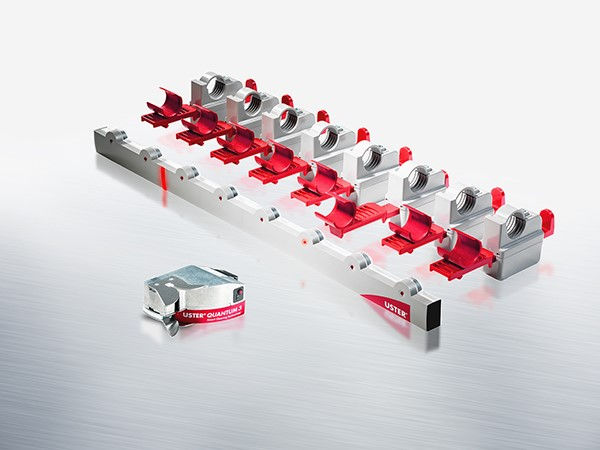
El purgado de los hilos es una forma eficiente de eliminar defectos, pero sería mucho mejor encontrar la causa raíz de las fallas y corregir los problemas en la fuente. Esa fue la solicitud de este hilador de tamaño mediano y orientado al futuro. El desafío era encontrar una manera de integrar el control de calidad dentro de los procesos de producción de hilo.
Solución USTER
La hilatura invirtió en el USTER® RSO 3D como una oportunidad para automatizar la prevención de reclamaciones de calidad y reducir el desperdicio en la hilatura de anillos. En la práctica, la hilatura logró:
• Evitar las husadas defectuosas en las bobinas finales
• Evitarla producción de baja calidad al tener virtualmente "purgadores en las continuas de hilar de anillos".
• Crear un mapeo de calidad de los husos individuales
USTER® RSO 3D se instaló en una sección de la hilatura donde las máquinas de hilar anillos están conectadas a Muratec QPRO EX con Spin Inspector. La hilatura tiene 40,000 husos en total.
Resultado # 1 - Evitar las husadas defectuosas con anticipación
La fábrica produce hilo de algodón peinado Ne 25. USTER® SENTINEL, basado en su inteligencia incorporada y varias mediciones, etiquetó el huso 336 como "fuera de estándar".
El número del huso afectado se pasó a la máquina bobinadora. La bobinadora Muratec QPRO EX está equipada con Spin Inspector e intercambiador de bobinas, por lo que la máquina pudo identificar al cop afectado durante la mudada.La husada fue retirada del proceso en la entrada de la máquina de bobinado, mientras que las otras husadas fueron transportadas por la cinta transportadora a las posiciones de bobinado. La husada rechazada fue luego inspeccionada en el laboratorio en un USTER® TESTER 6, con los siguientes resultados:

Si esta husada hubiera sido transportada y procesada por la bobinadora, habría habido un impacto severo en el nivel general de corte por cada 100 km, así como en la eficiencia de la máquina. También habría traído un alto riesgo de causar una costosa reclamación de calidad debido a demasiadas juntas y variaciones en la estructura del hilo. Estos factores confirmaron que etiquetar esa husada como "fuera del estándar" y expulsarla estaba justificado.
Después de recibir los resultados del laboratorio, un técnico de servicio verificó la posición 336 y descubrió que el recorrido estaba mal guiado, yendo por encima del espaciador de la barra de pasadores en lugar de debajo:
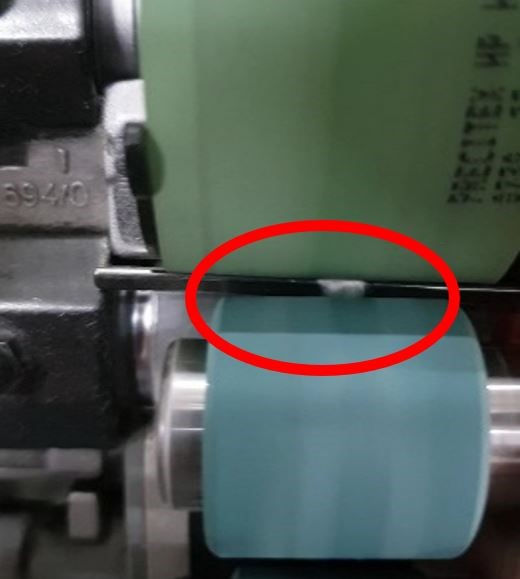
Encontrar tales posiciones de giro problemáticas sin ayuda o indicación adicional sería demasiado tarde o una cuestión de suerte. En ambos casos, el costo sería muy alto.
Según el propio cálculo de la hilatura, ¡cada mes la fábrica perdería la capacidad de producir 23 kg de hilo con solo este huso defectuoso! (Esto se basó en 12 mudadas por día a 65 gm por husada).
Resultado # 2 - detener la producción de mala calidad
Como parte de la evaluación, USTER® QUANTUM 3 activó una alarma CV en una posición de hilatura en particular después de dos desconexiones consecutivas del hilo de algodón peinado Ne 25. La alarma apareció en la CCU sobre la pantalla de la máquina, lo que indica que el huso 721 fue la causa principal del problema.
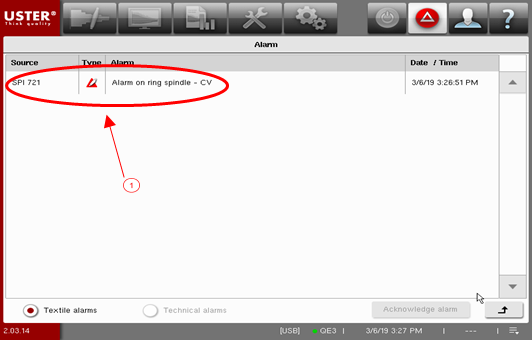
La CCU envió esta alarma a USTER® SENTINEL¸ donde la posición de hilatura se señalizó y se detuvo, ya que se instaló la opción Roving Stop.
Luego se retiró la husada y se verificó en el USTER® TESTER 6.

El técnico de servicio verificó la posición 721 para encontrar la causa raíz del defecto. Encontró que faltaba el delantal inferior en esta posición de hilatura.
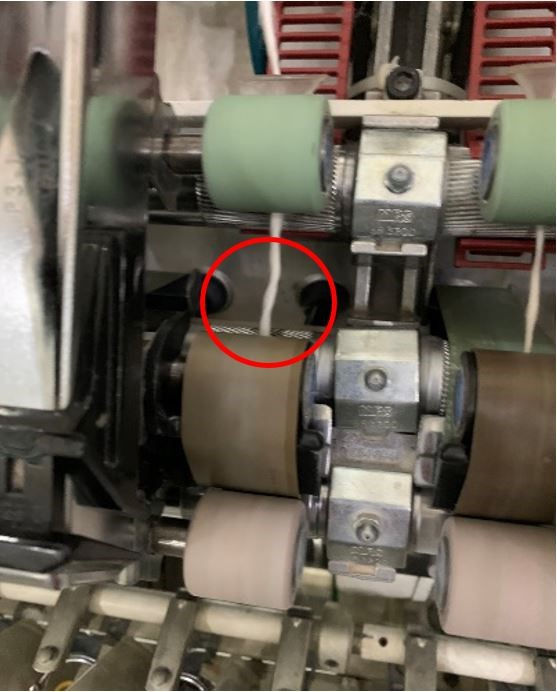
Como con el ejemplo anterior, identificar tales problemas es bastante difícil. Pero los costos continúan hasta que se solucione el problema.
Para este huso, la pérdida potencial de producción se calculó de manera similar al ejemplo anterior. Esto significa que solo por estas dos fallas, la hilatura perdería 45 kg de hilo por mes.
Cuando la hilatura extrapoló estos hallazgos en toda la operación, se concluyó que, con solo el 0.001% de los husos (estadísticamente) propensos a producir excepciones, ¡el negocio perdería alrededor de 95 toneladas métricas de hilo en un año!
Resultado n. ° 3: mapeo de calidad e influencias en las secciones de la máquina
En otra máquina, la hiulatura se enfrentó con un nivel muy alto de cortes PF (fallas periódicas). Además de la descripción general de la falla del hilo, la hilatura consideró el mapa de calidad en la CCU, que aparece inmediatamente después de que se haya procesado un desecho en el Muratec QPRO EX.
Centrándose en fallas periódicas, seleccionando PF en el mapa de calidad mostró que no se estaba afectando toda la hilatura, solo dos secciones particulares en el lado derecho de la máquina. Todas las posiciones en esta área se vieron afectadas, como se revela haciendo clic en las secciones.
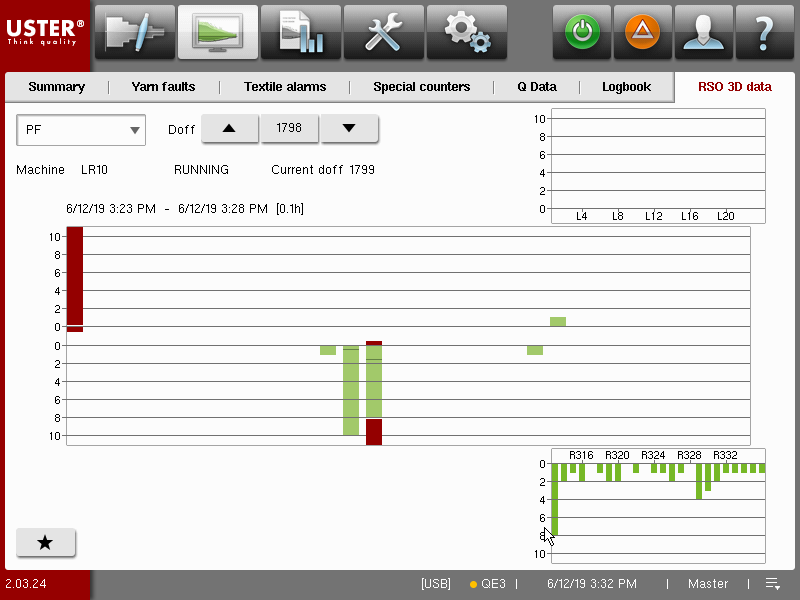
Equipado con esta información, el técnico de servicio comenzó a observar el área indicada. Inmediatamente descubrió que el polvo y los paquetes de fibras esponjosas caían sobre la máquina desde una aleta defectuosa sobre ella.
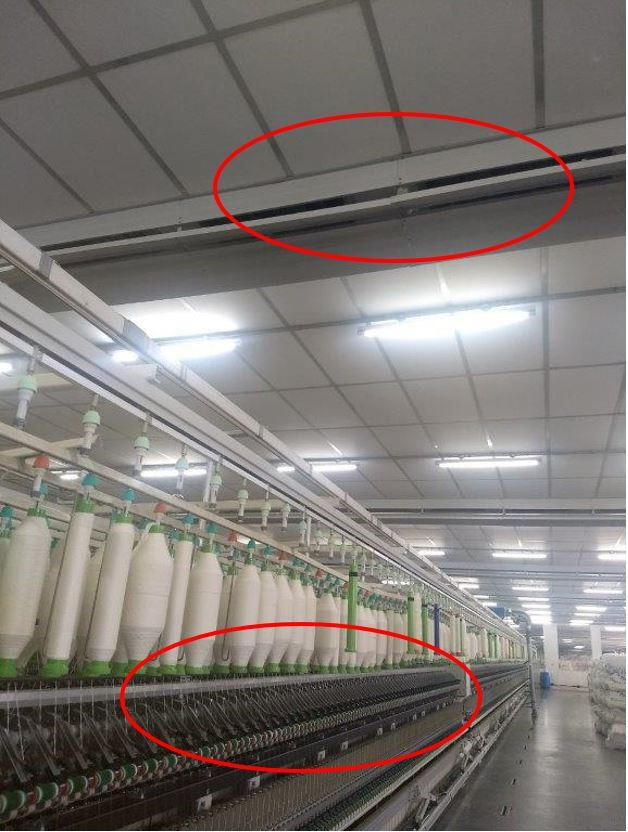
En este ejemplo, el problema de calidad creado por una aleta defectuosa podría haberse pasado por alto si no estuviera vinculado a un problema de hilo muy específico, como fallas periódicas.
La importancia del mapa de calidad es que puede relacionar fácilmente problemas tales como cortes, imperfecciones, desviaciones de CV y vellosidades con problemas reales en la máquina de hilar o el entorno de hilatura, que pueden identificarse y repararse fácilmente. Por lo tanto, puede ser utilizado por operadores y técnicos sin requerir un alto grado de experiencia textil.
Conclusión y resumen
El hecho de que USTER® RSO 3D fue fácilmente aceptado y utilizado por el personal de la fábrica aquí resultó en una reducción de las husadas bloqueados en el bobinado en un 90% después de un período de 1 mes.
El USTER® SENTINEL, el USTER® QUANTUM 3 y el USTER® TESTER 6 son equipos de nuestra representada:
Representamos a USTER TECHNOLOGIES AG, de Uster (Suiza) en exclusiva para España desde 2003
Disclaimer:
La información presentada en esta entrada es válida a la fecha de su publicación y, aunque se han puesto todos los medios posibles para evitarlo, puede contener errores de transcripción o traducción de la fuente original y no constituye ninguna garantía contractual. El fabricante se reserva el derecho de modificar las características de las máquinas y/o equipos detallados sin previo aviso.
©USTER TECHNOLOGIES AG. Todos los derechos reservados.
Media:
Para más información:
Miquel Fuster - miki@fuster.com
Comments